Asphalt vs Tarmac: What’s the difference?
Asphalt and tarmac are used interchangeably when discussing the design of roads. However, asphalt and tarmac are not the same and they are composed of different materials which makes them each suitable for specific applications. Asphalt is made from a blend of aggregates and bitumen and typically takes up to two days to fully cure. In contrast, tarmac consists of crushed stone mixed with tar and cures much faster.
In this blog, we’ll look deeper at the unique properties of tarmac and asphalt, the key differences in costs and reliability, as well as highlighting the pros and cons of each.
Here for something specific? Use the links below to find what you're looking for.
- What is asphalt?
- What is tarmac?
- What is tar?
- What is the difference between tarmac and asphalt?
- Summary of asphalt vs tarmac
- Why is asphalt used for roads?
- The pros and cons of asphalt vs concrete roads
- Improving asphalt roadways
- What are the most common types of asphalt?
What is asphalt?
Asphalt is a mixture of aggregates and bitumen and optional components such as polymers, fibres, or crumb rubber may be added to the mix to modify its properties. The high strength and durability of the material make it ideal for major and minor roadways, runways and cycleways.
Asphalt is an umbrella term that covers several mixes used within the construction industry and aggregate types can include gravel, crushed rock, sand or gravel. In asphalt pavement design all mixture types use bitumen as a binder to cement together the aggregate particle components. Over 25 million tonnes of asphalt are produced every year in the UK alone. With over 95% of UK roads and more than 90% of European roads using this material, asphalt is one of the most common road surfacing materials.
In the US, the term asphalt is used to describe what the rest of the world calls bitumen: the sticky black viscous liquid derived from petroleum that forms the binder in asphalt mixes.
What is tarmac?
Tarmac short for Tarmacadam, which refers to the road surfacing material made from a mix of aggregate materials such as sand and crushed rock which is bound together with tar. When compacted in place, tarmac forms a bound, strong and durable surface. Because of these properties, tarmac can be used on roads but it is more likely to be used in small areas such as household driveways.
Tarmacadam was invented by Edgar Purnell Hooley and patented in 1902. Adding tar to the aggregate enhanced the compacted macadam method introduced in the previous century, making the roads dust-free and more durable. Today, a bituminous binder will usually replace tar in the mix, and the material is then referred to as bitmac.
What is tar?
The tar used for tarmacadam is a natural black liquid substance. It can be extracted from the ground where it is found in large tar pits. It is also obtained as a by-product of coke production from the distillation of coal.
The use of tarmac for road making materials has receded, whilst the use of bitumen has become increasingly popular. This is due to the introduction and wider availability of bituminous products obtained from petroleum.
What is the difference between tarmac and asphalt?
As we’ve discussed, both asphalt and tarmac can be used for surfaces of roads, driveways and other trafficked areas, but they aren't the same material. Asphalt is a mix of aggregates and bitumen, whereas tarmac, or tarmacadam, is a mix of aggregates and tar.
Each differs in terms of strength, durability and finish and their application should be chosen according to the needs of the paving surface. Below you'll find a summary of the differences between asphalt vs tarmac.
Asphalt vs tarmac
Composition
- Asphalt is a mixture of aggregates and bitumen with the options of add-mixtures and modifiers to alter material characteristics.
- Tarmac is a mix of aggregates and tar.
Binder
- Asphalt is bound with bitumen of various grades which provides flexibility and strength.
- Tarmac uses modified tar which is less durable than bitumen.
Surface characteristics and finish
- Asphalt usually has a smoother surface but it is also available in coarse and porous mixes to help with drainage.
- Tarmac typically has a coarse, impermeable surface which makes it prone to water pooling.
Strength and durability
- Asphalt is known for its high strength and durability due to its flexibility.
- Tarmac is moderate in strength but it is more vulnerable to petrol and diesel spills.
Uses and applications
- Asphalt is commonly used for major and minor roads, runways, parking areas and cycleways.
- Tarmac is often used for domestic driveways, small parking areas and footpaths.
Mix temperature
- Asphalt is available in hot mix, warm mix, and half-warm mix options, allowing flexibility for application in different weather conditions.
- Tarmac is typically applied as a hot mix, which can be limiting.
Recyclability
- Asphalt is fully recyclable and can be reprocessed into new road surfacing.
- Tarmac is recyclable as unbound aggregate or as cold recycling technology in mineral cement emulsion mixtures.
Cost
- Asphalt can be more expensive if used for smaller surfaces.
- Tarmac is more cost-effective for smaller areas.
Reduce maintenance requirements and enhance the service life of asphalt pavements with Tensar's asphalt interlayers.
Learn More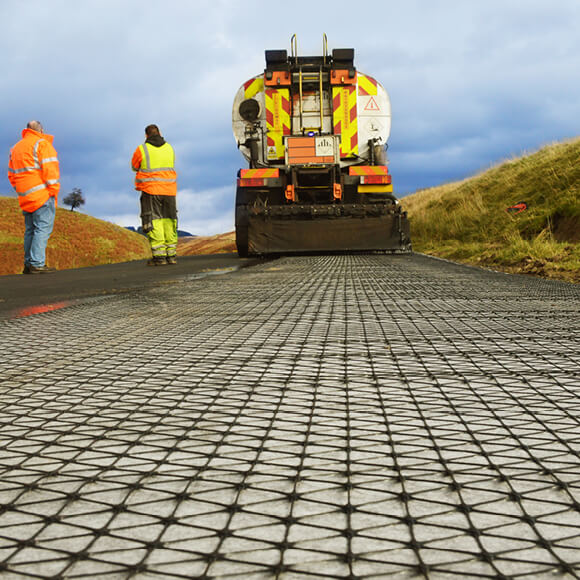
Why is asphalt used for roads?
Roads need strength and durability and asphalt is the most economical option for road surfacing. It is generally cheaper than concrete and more popular with road users due to its smoother ride and lower noise levels. Asphalt roads are constructed in layers and open to traffic quickly, minimising disruption; it can be milled, reprocessed, and recycled into new road surfacing, minimising aggregate usage and reducing whole-life costs.
The pros and cons of asphalt vs concrete roads
Installation time – Asphalt is quicker to install and with no curing time it can be open to traffic more quickly.
Cost – In most countries, asphalt roads are lower in cost to build but tarmac is generally more cost-effective for smaller surfaces.
Flexibility – asphalt surfaces are able to accommodate minor settlement and deformation.
Ambient Temperature – In hotter climates asphalt can rut or bleed whilst concrete is more tolerant. However, where seasonal temperature vary widely, concrete roads can have expansion issues.
Durability – In general, concrete surfaces are more durable and tolerant of high loading. Asphalt loses flexibility as it ages leading to fatigue cracking if not re-sealed. However, there are some newly developed asphalt technologies, like perpetual pavement or long-lasting hot mix asphalt pavement (US) that can perform beyond its design life, even up to 50 years.
Ease of Maintenance – a well-constructed concrete surface will require less maintenance than asphalt and have a longer life. However, maintenance of asphalt is relatively straightforward and can be done in small sections and reopened to traffic very quickly.
Ride quality – Road noise is lower for asphalt than for concrete (by about 3-6dB) and the ride quality is generally better.
- Recyclability – Concrete can be broken up at end of life and recycled as construction aggregate. Asphalt can be milled and re-cycled into new road surfacing. In some European countries already over 90% of reclaimed asphalt is reprocessed and re-used in new pavements.
Improving asphalt roadways
While asphalt roads have achieved proven success, they are not without problems: the surface is flexible but requires a stiff strong foundation, and when the foundation is insufficiently stiff, fatigue failure of the asphalt can occur much faster. The use of Tensar InterAx to stabilise road foundations improves the strength and stiffness of the road foundation, increasing pavement life and reducing whole-life cost. Tensar also offer full design support with Tensar+ which is intended to be used with Tensar InterAx in a variety of applications.
Existing asphalt roads may be resurfaced by milling off the upper asphalt layers and overlaying with new asphalt. In these circumstances any cracking in the lower layers would quickly reflect through to the new surface. Reflective and fatigue cracking can be controlled by introducing a Tensar asphalt interlayer product, such as Tensar AX5-GN, Tensar Glasstex or GlasstexPatch, prior to overlaying.
What are the most common types of asphalt?
Asphalt concrete (AC)
Asphalt concrete (AC) is the most commonly used asphalt material in the UK. Its strength comes from the use of an aggregate component with a smooth grading curve designed to have a high interlocking structure.
Hot Rolled Asphalt (HRA)
Hot Rolled Asphalt (HRA) is found almost exclusively in the UK is used for higher-speed roads. This material uses a gap-graded aggregate and the larger stones are bound together with a mix of fine aggregate and high viscosity binder. Stone chippings coated with a high-viscosity binder are then rolled into the surface to form a durable running surface.
Bèton Bitumineuse Très Mince (BBTM)
Bèton Bitumineuse Très Mince (BBTM), common in France, is asphalt concrete for very thin layers (AC-TL) of 20mm to 30mm, using a gap-graded aggregate to provide an open surface texture.
Stone Mastic Asphalt (SMA)
Stone Mastic Asphalt, sometimes called stone matrix asphalt (SMA). Developed in Germany and often used as a surface layer, this material is attractive due to its high deformation resistance and low tyre noise. It uses a gap-graded aggregate, and its strength predominately comes from the direct stone-to-stone contact in the structural skeleton of large stone particles. It is a very dense mix with a high mastic binder content comprising, modified bitumen, filler, and fibre.
Porous Asphalt (PA)
Porous Asphalt (PA) uses an open-graded aggregate mix bound together, leaving a high proportion of interconnected voids that allow free passage of water.
Warm Mix Asphalt (WMA)
Warm Mix Asphalt (WMA) has properties and performance levels similar to HMA, but with the advantage that the mix is prepared and laid at a lower temperature, saving energy and carbon emissions. Because of this, there is growing interest in the use of these warm mix asphalts for environmental reasons.
Next steps
Found this article useful? You may also want to read:
Have an upcoming project and require expert support? our design team are here to help.
Get in touch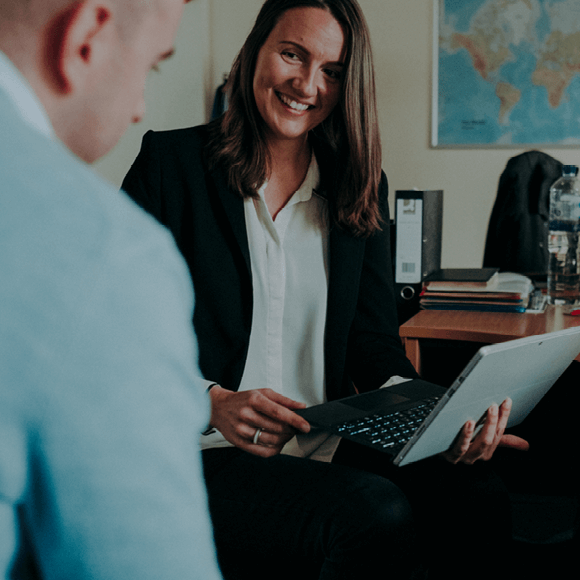