Different Types of Aggregate, Their Uses, and Sizes
by Matt Brown, on August 29, 2024
Screening separates aggregate into particle size fractions (source - Powerscreening)
Aggregates are essential for civil engineering construction. They are hard, granular, mineral materials, used on their own or with the addition of cement, lime or bituminous binders. They are utilised across all forms of infrastructure and are a critical component in roads, concrete structures, and coastal protection. In this guide we look at the different types of aggregate and their uses. We will also cover the increased use of manufactured and recycled aggregates.
Use the links below to navigate to specific sections of interest:
- What are the different types of aggregate?
- Primary versus secondary aggregates?
- What are aggregates used for?
- How are aggregates classified?
- Aggregate types and their applications
- Mechanical stabilisation of aggregate layers
Want to chat about how Tensar solutions could benefit your project? Contact us now to speak to our friendly team today.
What are the different types of aggregate?
Aggregates fall categorised into three types based on where the minerals are sourced from: natural, manufactured, or recycled. Materials include sand, natural gravel, crushed rock, Type 1, recycled asphalt, crushed concrete, and Type 6F2. Common specifications for aggregate in UK highways and construction include Type 1, Type 6F2 and Type 6F5.
Read on to discover more about these aggregate categories – and the ways in which the various aggregate materials can be used.
Natural aggregates
These are composed of rock fragments that are mined, quarried, or dredged and used in their natural state or processed by crushing, washing, and grading by particle size. This group includes crushed rock, sands, and gravel.
Manufactured aggregates
These are produced from an industrial process, often as a by-product of the primary process, where mineral material undergoes change involving thermal or other modification. Such aggregate products include iron and steel slags, and ash. Some material may undergo secondary processing. An example would be lightweight aggregates produced from fly ash, a by-product from coal-fired power stations that is heated to high temperatures to create hard, rounded pellets.
Recycled aggregates
These result from the reprocessing of materials previously used in construction. Examples are, building demolition waste, used railway ballast, and reclaimed asphalt arising from road resurfacing works.
Primary versus secondary aggregates
In the UK, aggregates are often categorised into two main categories: primary and secondary aggregates.
Primary aggregates
Primary aggregates are natural minerals extracted specifically for construction purposes. This category includes all natural aggregates such as; sand, gravel, and crushed rock extracted from quarries.
Secondary aggregates
Secondary aggregates include manufactured and recycled materials, as well as by-products from other mineral extraction processes, such as colliery spoil. This category of aggregats is increasingly utilised to enhance sustainability and reduce environmental impact.
What are aggregates used for?
Aggregates may be used on their own or in a composite, where aggregate particles are bound together with cement, lime, bitumen, or resin. Humankind has utilised aggregates for infrastructure and to construct our built environment since the Bronze Age. Massive volumes of aggregate are consumed by today’s construction sector, with applications in roads, railways, bridges, buildings, and other structures.
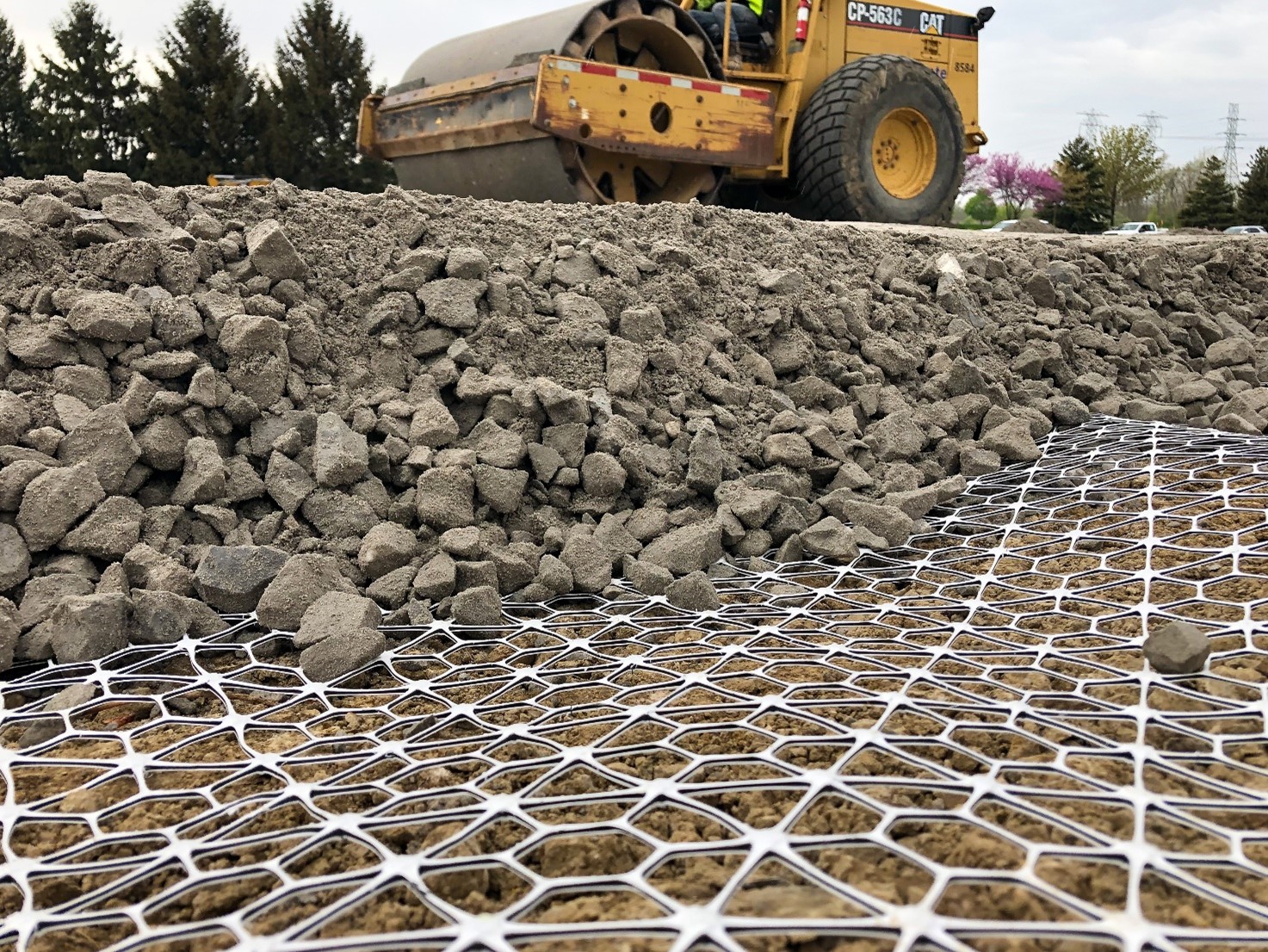
Tensar InterAx has optimised geogrid geometry to enhance the stabilising effect on the aggregate to provide a mechanically stabilised layer
Road foundations
In road construction, aggregate types are essential for different layers of a pavement. For a capping layer, ‘lower grade’ aggregate may be incorporated over weak soils. The main support layer, the subbase, is constructed from a good quality aggregate selected to provide a stiff foundation. In some cases, a structural base layer of high quality, carefully graded aggregate, will be used above the subbase to provide a dense, strong, stiff layer to support the asphalt or paved surfacing.
Rail trackbed
In rail track construction, different types of aggregate are used to created a stable foundation. Ballasted track construction may incorporate a sand layer at the base to reduce water pumping. The foundation layer, the sub-ballast, will typically be a graded aggregate, performing a similar function to a road subbase. The ballast layer, of single size aggregate, supports the sleepers (rail ties) and distributes load down to the foundation. Visit our railway track reinforcement page to discover more.
Asphalt
Asphalt, or asphalt concrete, is a familiar material providing the smooth road surfaces on which we drive. Asphalt is distinct from tarmac, and comprises a mix of aggregate materials bound together with bitumen. Other components may be included to modify and improve the asphalt properties.
Concrete
Concrete has been around as a construction material since 6500 BC. Aggregate particles are bound together with a cementitious paste to form a rock-like material. What we call concrete today is typically produced using Portland Cement. Modern concrete can have extremely high compressive strength. It typically comprises 60%-80% aggregate types by weight.
Reinforced concrete, where steel is incorporated to provide the necessary tensile strength, is the backbone of the construction industry. It is used in foundations, tunnels, drainage works, buildings, dams, and bridges. In fact, just about every construction project will incorporate concrete somewhere. High quality, crushed rock aggregates are required for concrete production.
Drainage
Aggregates with limited fine particle size content will have large contiguous voids when compacted. This allows water to pass freely through the aggregate, highlighting the importance of drainage in construction. Drainage aggregates are used to create pathways for water and other liquids. Trenches filled with drainage aggregates are constructed alongside roads and railways to lower groundwater levels and remove stormwater.
They play a vital role in Sustainable Urban Drainage Systems (SUDS), helping to regulate stormwater and in waste containment lagoons for leakage collection. To maintain flow capacity and prevent contamination, geotextile separators often protect the boundary between soil and drainage aggregate.
How are aggregates classified?
As with all construction products, aggregates must be classified and have characteristics relating to specific functions and applications. The classifications of aggregates are typically defined by origin or source, particle shape, particle size, and density.
Origin
The different aggregate types and their origin are classified by their source, which can be primary or secondary. The chart below provides a summary of the various aggregate sources, illustrating the differences between primary and secondary aggregates.
Table 1 - Classification of construction aggregate by their origin or souce.
Shape
The shape of aggregate particles influence how they interact under load and how densely they pack together. Angular particles, typical in crushed rock aggregate, will interlock and have a higher shear strength compared to rounded particles, which more easily slide against each other. For drainage, aggregates with rounded particles, such as river gravels, will be advantageous as they have a greater void content (the space between particles) compared to aggregates with interlocking angular particles. For concrete use, aggregates with rounded particles give better workability, while angular aggregates lead to higher strength concrete.
Density
The density of aggregate materials will directly relate to the weight. For some applications, lightweight aggregates have an advantage. For example, earthworks structures constructed over weak soils can lead to bearing failure of the foundation soil. The use of lightweight aggregates reduces the bearing pressure and reduces the potential for failure. Similarly, the use of lightweight aggregates can significantly reduce the settlement of earth structures. Lightweight aggregate has been used as a structural fill in TensarTech reinforced soil walls to reduce settlement and improve performance.
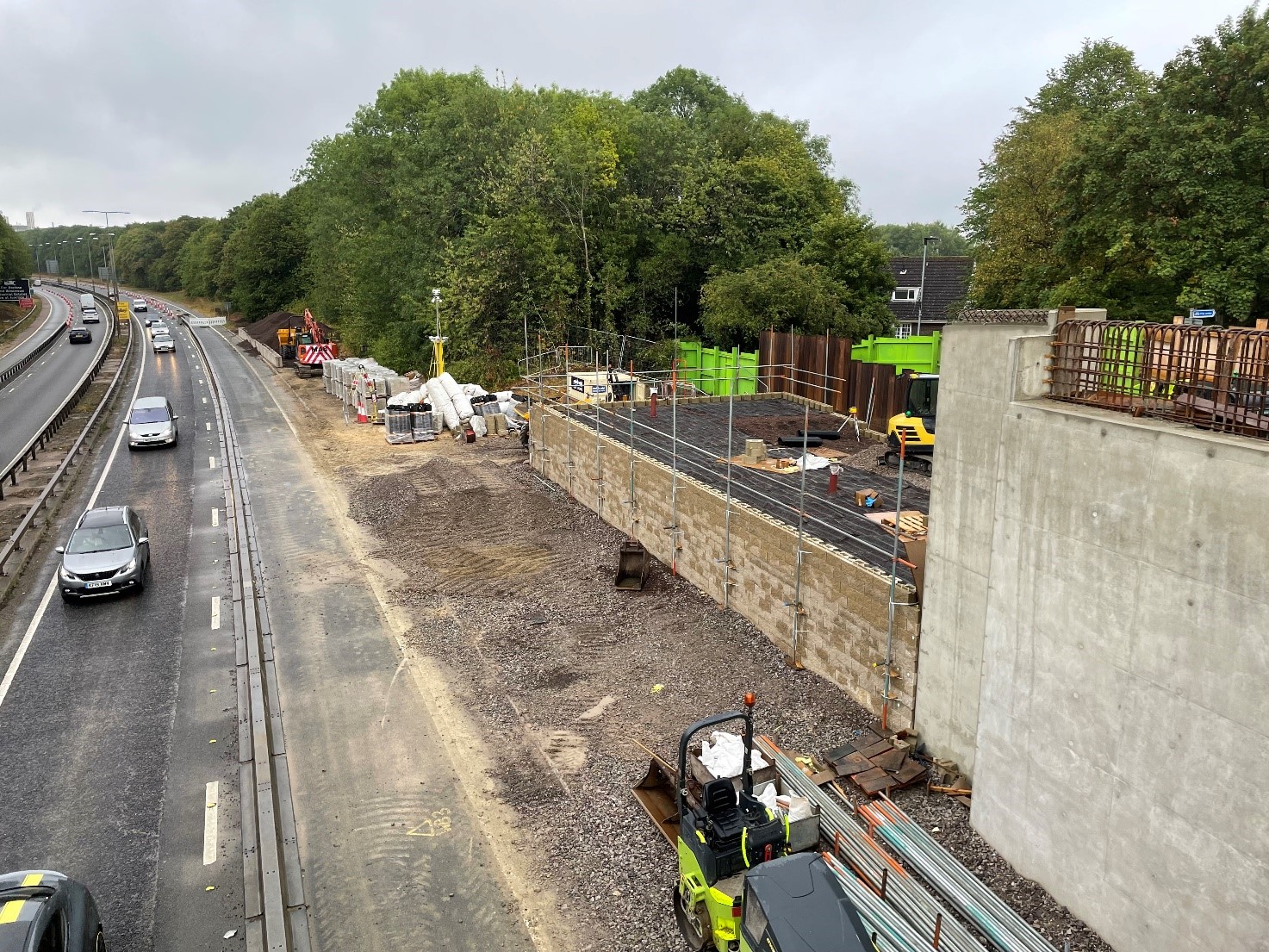
Construction of the A47 Longthorpe Footbridge where this TensarTech structure required complex geometry and lightweight fill to create wheelchair friendly shallow access ramps within a very restricted space.
Size
Particle size and particle size distribution (the proportion of soils in each size range) have major influence on shear strength, compacted density, and permeability of soil or aggregate. As a result of this, particle size distribution parameters for aggregates are specified during road construction projects, highlighting the lower and upper bound limit for each particle size.
Concrete
The particle size used in concrete mixes will vary, but typically it will comprise a mix of fine aggregate (<4.75mm size) and coarse aggregate (usually 9.5mm-37.5mm size). A coarse aggregate of 20mm size is most commonly used for reinforced concrete, with a larger 40mm size for mass concrete.
Road subbase
The compacted subbase layer must be dense, with a high shear strength to distribute load onto the formation. The aggregate will comprise a mix or particle sizes designed to create the necessary compacted density and shear strength. Typically, particle size will range from 31.5mm down to 1mm, with only a small fraction in the silt/clay range (<0.063mm). In the UK, particle size distribution for highway works is defined in the Manual of Contract Documents for Highways Works, Volume 1 Series 800.
Aggregate types and their applications
Understanding the various types of aggregates and their specific uses is essential for effective construction. This section delves into the characteristics and applications of different aggregate types.
Sand
Sand is obtained from open pits or by marine dredging. Sand results from the weathering and erosion of rock. Accumulated deposits are formed by the action of wind, glaciers, and rivers. Most sand particles are durable fragments, rich in silica. It can be classified into two main types:
- Superficial deposits - These are recent deposits formed by rivers within the last two million years, located in river valleys or elevated terraces. These deposits are generally clean with low silt and clay content. Deposits from glacial meltwaters may contain higher levels of silt and clay.
- Bedrock deposits - These are older formations dating from the Permian to Paleogene periods, offering different properties compared to superficial deposits.
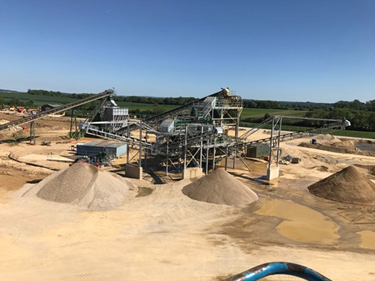
Sand screening plant - seperating by particle size (source Centristic)
Uses of sand
Sand used in construction is categorised by particule size rather than mineral composition:
Table 2 - Sand particle size range
Sand aggregates are an essential component of concrete mixes and cement mortars. Sand is also used as a filter medium, as a levelling layer beneath block paving, and incorporated in some asphalt mixes.
Natural gravel
Similar to sand, gravel is also obtained from open pits or by marine dredging and consists of durable rock fragments. Its sources include:
- Superficial deposits - Found in river valleys or former riverbeds, often containing low silt and clay content. Glacial deposits may have higher silt and clay.
- Bedrock gravel - These gravel deposits occur as bedded formations, often loosely compacted and easily excavated.
- Marine deposits - These are deposits formed by rivers and glaciers but later submerged due to post-glacial sea-level rises (an important source of gravel in the UK).
Uses of natural gravels
Gravel is classified into fine, medium, and coarse sizes.
Table 3 - Gravel particle size range
Natural gravels are used as a fill material, as backfill to buried structures and in capping layers as part of a road foundation. When washed and graded by particle size, natural gravels can be utilised in concrete mixes and as a drainage aggregate. After crushing and grading, natural gravel can be used as a road subbase.
Crushed rock
Crushed rock aggregate is now the most common source of primary aggregate in the UK. After quarrying, the rock is crushed and separated by particle size. The various particle size fractions can then be combined in the correct proportions to meet specific grading requirements for the different applications. One quarry source can then supply suitable aggregate mixes for use in concrete, subbase, asphalt, drainage, and other applications.
Uses of crushed rock aggregate
The strength and angular shape of crushed rock aggregates make it ideally suited for high strength concrete mixes, road subbase, rail ballast, asphalt concrete, and surface dressing applications.
Type 1 aggregate
It is very common to see reference to Type 1 aggregate. It is a well understood and readily available aggregate mix. Type 1 refers to a specific aggregate specification found in the UK Manual of Contract Documents for Highway Works – Volume 1, Specification for Highway Works. Series 800. The particle size distribution (grading curve) is smooth and broad, with a maximum particle size of 63mm and 99% passing the 31.5mm sieve size, The silt/clay content is limited to a maximum of 9%. The smooth broad grading curve ensures a high compacted density.
Uses of Type 1 aggregate
Type 1 aggregate is a premium material. It is used to provide a strong stable foundation layer for roads. It may also be specified for working platforms and unpaved access roads.
Figure 1 - Type 1 Aggregate Figure 2 - type 6F2 Recycled Aggregate
Recycled asphalt
Road resurfacing often entails planning off the upper layer of road surface prior to overlaying with new asphalt. The plannings are a useful source of aggregate.
Asphalt arisings from resurfacing are valuable aggregate resource (source MGL Group)
Uses of recycled asphalt
Asphalt planings (or arisings) are suitable for recycling into new asphalt. At the batching plant, the recycled component is incorporated into the asphalt mix in place of a proportion of primary aggregates. Asphalt arisings are also useful as road subbase material. The UK Specification for Highway works includes a specification for Type 4 aggregate (asphalt arisings) for use as unbound aggregate in roads.
Crushed concrete
Concrete from demolition can be crushed and separated into particle size fractions, then re-combined in the appropriate proportions for specific applications.
Uses for crushed concrete aggregate
Crushed concrete aggregate can be used as an alternative to crushed rock aggregates in concrete and the unbound layers in road construction. It can also be used for asphalt concrete although consistency may be an issue due to variations in the source of crushed concrete.
Type 6F2 and Type 6F5 aggregate
Type 6F2 and Type 6F5 refer to selected granular fill material, including recycled aggregates, defined in the UK Manual of Contract Documents for Highway Works – Volume 1, Specification for Highway Works (Series 600). The differences between these two types of aggregate can be summarised as:
- Type 6F2 consists of crushed demolition materials, such as concrete, brick, and mortar, with a maximum particle size of 125mm and at least 80% passing through a 90mm sieve. Grading is based on Table 6/2 of Series 600, and it is tested per BS 1377
2. Imported materials of this type are classified as Type 6F5. - Type 6F5 is a selected fill material imported to site, with grading similar to Type 6F2 but defined in Table 6/5 of Series 600 and tested to BS EN 13285. It can include natural aggregate, crushed concrete, brick, incinerator bottom ash, slag, and mine waste.
Uses of Type 6F2 and Type 6F5 aggregate
Both types are commonly used as a fill material for piling mats and working platforms to support cranes and other plants. They are also used as a capping layer in road foundations over weaker soils, partially replacing more expensive subbase aggregate.
Mechanical stabilisation of aggregate layers
As we learned above, compacted aggregate layers form the foundation of most road pavements and access tracks. Well compacted aggregate layers distribute the loading and reduce the bearing pressure on the subgrade. The strength and stiffness of an aggregate layer can be increased by incorporating a stabilisation geogrid, such as Tensar InterAx geogrid.
Mechanically stabilised aggregate - using Tensar InterAx geogrid
The aggregate particles interlock with the geogrid apertures and are confined by the geogrid. The particle confinement prevents movement and rotation of the particles, stabilising the aggregate and increasing shear strength. This in turn, increases the bearing capacity of the layer. This is known as a mechanically stabilised layer (MSL).
Ready to discuss how Tensar solutions could support your project? Get in touch today.