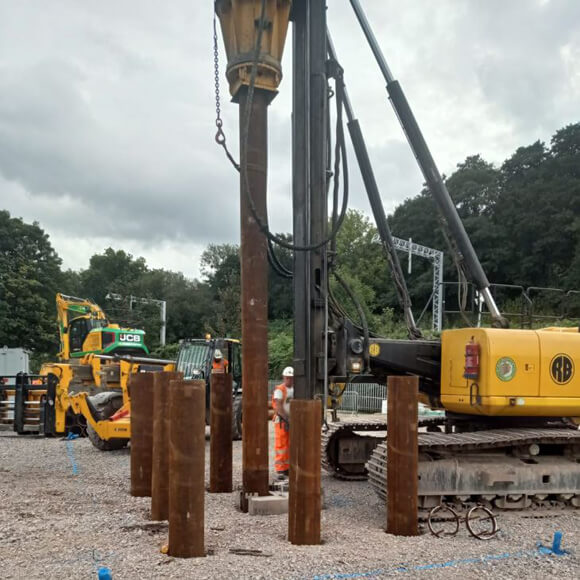
Mobile crane and piling rig working platform
Geotechnical investigation showed a contaminated and very low-strength cohesive subgrade material, with a worst-case undrained shear strength (cu) of 5kPa. The subgrade parameters meant traditional design methodologies were unable to provide the necessary factors of safety within the design.
Benefits
- Development of a viable solution where other methods would not work
- A collaborative approach involving Tensar’s design know-how to develop a technically competent, safe and cost-effective solution
- A third party ‘category 3’ design check successfully undertaken by design partners
The client required a stabilised working platform solution on a low-strength contaminated subgrade in tight timescales, as an alternative to a significantly costly ground excavation and replacement exercise. It was also paramount that the solution was able to meet the critical path piling activity programme and minimise expenditure in time, cost and carbon emissions.
Tensar’s T-value method provided an engineering solution to use for geotechnical parameters that fell outside the constraints of the widely adopted BR470 method (suitable for cohesive subgrades of 20kPa<cu<80kPa). Safety was ensured through both uprating plant loading and the design methodology itself, which is underpinned by significant derivation and validation testing (Lees 2020, Lees & Matthias 2019). The platform was safely and efficiently constructed, tested and used for the duration of the piling workings, despite the challenging project conditions.
Luke Winch, Senior Design Engineer at Balfour Beatty Rail stated,“Tensar was the only viable solution given the incredibly poor ground conditions, where alternative solutions meant removing a significant volume of material to be replaced by granular fill. This presented technical challenges and significant cost, given the land was also contaminated. Tensar’s reinforced working platform limited the volume of material to be removed and sent to landfill.”